Information Management: Can WES get predictive?
都是关于orchestr仓库执行系统ating busy fulfillment centers in the here and now. Some WES solutions are moving into more predictive capabilities that simulate what is likely to play out in the near future, recommending actions. It’s all part of the fast-evolving WES solutions space.

Latest News
C&B Material Handling acquires new forklift dealership groups Single-Carrier vs. Multi-Carrier Shipping Stategies Frazier mourns passing of Domenick Iellimo, EVP at the company Driving the Risk Out of Line Haul Fleet Management with AIoT Technologies RoadOne IntermodaLogistics announces acquisition of The Transporter More NewsLatest Resource
Single-Carrier vs. Multi-Carrier Shipping Stategies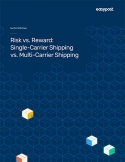
All Resources
When it comes to real-time orchestration of fulfillment center processes,warehouse execution system (WES)software has come to the forefront as a system that promises a nimbler way of releasing and managing work to create a productive operational flow.
WES software uses its near real-time ties intoautomated materials handlingand control systems to gauge issues like machine availability, as well as order fulfillment progress and service level cut off times, to decide how to release orders and sequence work through a facility.
But is “real time” all that WES is cracked up to be? Can WES solutions evolve into something more predictive in terms of how processes and resources need to be adjusted so warehouse flow stays productive, while new orders dropping into the process will hit shipment cut-off times? Some vendors say WES is already getting more predictive and gaining richer analytics, though WES dashboards and metrics that show what is happening in the here and now remain essential.
WES is a rapidly evolving category of software that sits between traditionalwarehouse management systems (WMS)and automated materials handling systems like conveyors, sorters, put walls, shuttles or other types of automated storage and retrieval solutions, as well as robotics.
WES solutions are used to handle order release and manage material flow, not only through order release and orchestration logic, but also through dashboards and metrics that give busy managers insight into production rates, picking productivity, and abnormal events or trends.
WES intelligence gets applied on a couple of different levels, saysDan Gilmore, CMO withSofteon, which offers both WMS and WES software. First, it handles continuous order release based on factors like its knowledge of automation and human resource availability, current flow and workloads, and shipment cut off times for orders coming in. Gilmore adds that Softeon’s WES can also run simulations based on all the factors the WES is monitoring and recommend adjustments like reallocating labor to different areas when needed.
“即使一个公司有一个先进的WMS和良好哒shboards on current warehouse productivity, supervisors still spend a lot of time looking at all kinds of data to try to arrive at good decisions,” Gilmore says. “There’s just so much data to consider—inventory information, order information, replenishment data, and available machine and labor resources—that it becomes very challenging to process all this data and make those adjustment decisions by just looking at metrics. Ultimately, few managers can assess all the information and arrive at good decisions as effectively as a smart WES can.”
Predicting pinch points
In Softeon’s WES, says Gilmore, a dynamic rules engine provides the software intelligence to handle automated order release, but the WES’s intelligence is also at play in simulating what might happen later in a shift. Such simulations work over a time-phased, hourly horizon by process area or zone, explains Gilmore, projecting when certain areas might be over-staffed or understaffed, and recommending adjustments, such as adding people to a picking process, or a packout process, or opening up more resources like additional put-wall modules or pack-out areas.
“This capability allows you to realign those resources from places where you will be overstaffed to places where you are understaffed, and it can do that automatically. A lot of companies will start out with the system, first making a recommendation until they get to really trust the system. But once they see the system is consistently making good decisions, they let it go to full autonomous mode [on such dynamic resource adjustments],” says Gilmore.
WES vendors vary in their capabilities, says Gilmore, so while continuous order release capability is fairly common among WES vendors, don’t expect every WES solution to be able to perform time-phased simulations. But such ability to look ahead and guide managers on what to do as the day unfolds is going to be increasingly important, Gilmore predicts. “WES is always listening, if you will, to what is happening in the warehouse, and using that to make smarter decisions. That is why WES is central to the concept of the smart warehouse of the future.”
Because WES integrates with both WMS and WCS, it has a real-time handle on the order pool, inventory consumption, and progress of work through automated zones. This broad scope makes WES dashboards useful for managers who need to keep tabs on warehouse productivity, potential bottlenecks, and the progress of order fulfillment work.
Mary Elliott, chief product and technology officer forFortna, says the company has been enhancing the dashboards and KPIs for its WES solution, and also augmenting the intelligence layer of the WES so it can spot trends and recommend adjustments on its own. “Improving the dashboarding and KPIs is part of our focus, but the next evolution with WES intelligence, we believe, is about the system being able to adjust itself based on what the data is indicating,” says Elliott.
WES dashboards are still highly useful, Elliott says, but Fortna is enhancing their WES’ orchestration engine, using artificial intelligence and machine learning technology, so it can determine the best adjustments, rather than expecting managers to spot needed alterations on a dashboard. “We’re working on a true orchestration engine that continuously balances the flow of a warehouse, bringing in some machine learning and AI aspects. The idea is not only to monitor the flow and performance of the warehouse, but also adjust based on what is happening.”
For example, says Elliott, a WES solution that monitors a goods-to-person automation system could identify that a couple of the operators working with the system are falling behind the expected pick rate, and recommend adjustments, such as sending some orders to a different workstation until the flow balances out. WES intelligence of this type will be increasingly useful for DCs, says Elliott.
“仪表板多年来一直提高,以前sent useful KPIs, but now as the systems get more integrated, and you have all these zones of automation or mobile robots running around, there is just more complexity that influences flow,” Elliott says. “As a result, it’s getting harder and harder for a manager, even with good dashboards, to understand how all the information ties together in a way that leads to good decisions. This complexity is why it’s important to drive some of that intelligence into the WES, and the way it orchestrates the operation. It can be looking at all these variables to arrive at better adjustments than a human could, particularly with machine learning over time, just because there is so much data and interconnected systems today.”
According to Elliott, the extent to which a WES can do this type of “intelligent coordination” is going to be at the forefront of WES going forward. WES solutions have always done some orchestration when releasing orders, Elliott adds, but orchestration within WES and the ability of a WES to essentially self-adjust can still be improved.
“The most important thing we are doing is advancing that ability for the WES to intelligently respond in real-time based on what’s happening in the system,” says Elliott.
Dashboards matter
The user interface (UI) and dashboard tools of a WES solution remain extremely important, even without predictive capabilities.
Just knowing the state of current warehouse and pick rate effectiveness, and getting alerts when something starts to go astray, remains a core area of functionality for most WES solutions. This is especially true with more DCs taking on e-commerce fulfillment responsibility that involves specialized picking zones, and all the complications of properly replenishing and staffing areas that could become bottlenecks that cause an operation to fall short of service levels.
“The growing volume of e-commerce activity is making it more important for DCs to have real-time insight on error notifications and overall system performance. Am I going to make my shipping deadlines? Is there a system-related issue that will prevent me from hitting our service targets? Can I rebalance the workload to increase the overall warehouse throughput? Live information and alerts on an intuitive WES dashboard are becoming more and more important for our customers,” saysJoe Colletti, CEO and president of DMW&H, which offers theirShiraz softwareat the WCS/WES level.
“One of the bigger trends is the progress around user interfaces, dashboarding and monitoring functions,” says Colletti. “With today’s volumes, there is limited time for problem discovery; it is all about problem anticipation, notification and resolution. Our systems need to immediately alert our customers about pending or actual problems and display them in a way that allows quick identification and resolution. In some cases we can even include pop-up menus that provide advice on troubleshooting initiatives. For our customer service and support organization, the dashboard also plays a vital role in allowing remote access for troubleshooting as well as proactive assessments of system performance and trends.”
According to Colletti, DMW&H’s Shiraz WCS is typically used when there is a WMS in place, and transitions into a WES if the WMS is lighter in functionality or does not exist at all. “It’s always important to adapt our WCS/WES solutions in a way that meets our customer’s unique requirements.”
Configuring the operational flows and processes a WES governs, and setting up its UI, dashboarding and metrics should be easy to set up, according to Ed Romaine, vice president of marketing and business development with New Dawn, a unit ofConveyco. WithNew Dawn’s Horizon WES, the utility for setting up a DC’s specific material flow is done using a Visio-like tool to speed up the configuration.
Is an analytics layer needed over WES?
Warehouse execution system (WES) vendors have been augmenting their features for dashboarding and operational insights, but can one system really analyze and apply intelligence to all the factors that influence the effectiveness of a modern fulfillment center?
一个相对较新的供应商Cognit-Ops th的赌注at companies with warehouse fulfillment operations will see the value in anartificial intelligence (AI)powered decision support layer.
TheCognitOpssolution connects with WES data, as well data from other systems, to create what the vendor says can be thought of as a “warehouse operating system” that leverages predictive capabilities and AI to arrive at tangible action items for managers, according toRoger Counihan, chief revenue officer for CognitOps.
“We are a believer in the value of WES solutions, which are really good at sensing and planning everything within their scope and control, but there are so many different systems and factors that influence a fulfillment operation, that operations can benefit from a continuous intelligence layer on top of all their systems, which is where CognitOps fits in,” Counihan says.
“Our solution does sit on top of automation systems, but is also looking at other systems like a labor management system or a transportation management system, to connect all that data and provide a forward-looking forecast. Our software is using that information to determine: What do we think will happen next, and what adjustments should be made to optimize the overall performance of the building?”
Rather than just metrics, even dynamic ones that get updated frequently, the CognitOps software presents management with a set of actions to take based on what the AI and logic in the software is predicting will happen. It’s predictive and prescriptive in nature, rather than a dashboard in the conventional sense of WES or warehouse management system dashboards, explains Counihan.
“When they log in to our system, there’s connected data from different underlying systems that gives them an overall perspective on how their building is doing, but there’s also a list of management prescriptions or notifications, which need action,” he says.
Currently, he adds, while WES vendors are enhancing their dashboards and analytics, CognitOps sees the biggest alternative to what it does as being in-house data science teams using AI tools, rather than vendors with WES solutions.
The tool also populates the WES with the appropriate configuration data for underlying automation to be governed by the WES. Additionally, says Romaine, the WES has “emulator” tools that are used to stress test how the system will run after go-live from an information technology performance standpoint, even if volumes double or triple. “With our software, you are building a dynamic and live system that reflects how the system will perform on go-live,” Romaine says. “Our emphasis is on a WES that is ready to go from the start, based on your operation’s unique profile.”
When it comes to dashboarding, New Dawn uses drop-down selections and other non-programmatic features to allow rapid setup of metrics, which can be added to or modified later as needed.
“With dashboarding, there are certain metrics like units per hour, ‘no reads’ [at bar code scan points], or production rate, that nearly everyone wants, but others are going to want special metrics, which is why it needs to be easily configurable,” Romaine says. “Our dashboards do get used heavily, because managers know what the norm is for their areas of responsibility. They can use a WES dashboard to see if the production rate is slowing down, and where. Or if no read events start to happen at a scan point at a rate that is well above the norm, they’ll know that’s something that needs to get checked out immediately as a likely maintenance issue.”
Predictive maintenance
Sean Brown, senior manager of software development forMHS, says dashboards and metrics are one of the most impactful aspects of a WES, in that managers use them on a daily basis to gauge operational effectiveness, potential bottlenecks, or to look for possible maintenance issues.
“Ultimately, one of the most important things about WES dashboarding for the managers in operations is that it provides them with a means of taking a real-time look at key concerns like, ‘how healthy is my system running right now?’ or ‘how well am I running in terms of orders meeting my cut-off times?’ or, ‘how productive are my people right now?’ or as we get more into mobile robots, ‘how productive are my robots right now?’”
MHS offers WES software, but also offers software for predictive maintenance developed by a different group within MHS. The two are different applications, though they do have the same look and feel, and additionally, says Brown, predictive maintenance insights can be made part of a unified dashboard that includes WES metrics and alerting.
“As an organization with a support role, predictive maintenance capabilities are something we push pretty hard to achieve because we are trying to head would-be issues off at the pass before they become problems that cause downtime,” says Brown.
As for predictive WES functions focused on operational what-if scenarios, Brown says that hasn’t been a focus in MHS’s WES, not to the extent of functions like dynamic order release and real-time orchestration of warehouse floor and bottleneck issues, which is supported by KPIs and dashboarding.
This is where much of the value lies for WES users, Brown says, especially those moving from older WMS solutions that lack functions like continuous order release and visibility into automation data and workloads.
Advanced analytics
Dashboarding functionality has been part of WES software for many years, evolving in ways that include mobile device compatibility as well as advanced analytics that can tie into data from multiple systems, according toBart Cera, president and COO of VARGO, a warehouse automation integrator and WES provider.
WithVARGO’s COFE(Continuous Order Fulfillment Engine) WES, for example, its user interface is now Web-based, allowing for easy access to WES dashboards and metrics from mobile devices such as smart phones and tablets.
“VARGO has gone through a bit of an evolution with our WES, when it comes to dashboarding,” says Cera. “The first step in this evolution was enabling mobile access, so WES dashboards and performance metrics are easily available to any manager or executive anywhere, on their phones and tablets. This brought our WES out of the distribution center—and mainly something for supervisors use—to supply chain executives that can now access data on their devices anywhere.”
Additionally, explains Cera, VARGO has embedded a top-tier analytics engine into COFE that allows users to pull in data from multiple systems and databases to gain valuable insights into issues like a more refined cost of warehouse fulfillment, which might involve current operating data from an external payroll system outside of the WES, for example. By having the analytics engine integrated into COFE, says Cera, WES users can build their own analytics dashboards without having to turn to a consultant, or put an analytics request into a queue of projects that an internal business analyst would generate using some other stand-alone analytics engine.
“At the distribution center level, users haven’t typically had the ability to generate this type of higher-level analytics as it pertains to the warehouse,” says Cera. “They’d have to farm that out, which takes time. Now they have that analytics capability right within the WES, which we feel was an important second step in the evolution of WES’s dashboarding and reporting.”
While there are some predictive aspects to WES analytics, adds Cera, the overall intent with VARGO’s WES is to provide actionable insights on trends that will impact the distribution center’s performance, rather than perform complex simulations.
“We’re focused on decisioning and action items that affect building flow,” adds Cera. “Analytics can help you understand expected work rates versus actual work rates by shift, or by components of a shift, to better help you do your planning and your labor allocation. We also look closely at SKU movements within a facility, to do things like drive out the number of touches, or reduce travel time relative to where SKUs are placed. Understanding SKU movements help ensure you have the right inventory in the right locations and in the most appropriate storage medium or automation. These are all crucial elements to maximize the amount of product flowing through your building and with the least amount of necessary staff possible.”

About the Author

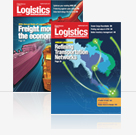
Subscribe to Logistics Management Magazine!
Subscribe today. It's FREE!Get timely insider information that you can use to better manage your entire logistics operation.
Start your FREE subscription today!
Article Topics
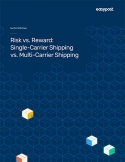
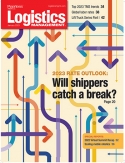
LM Viewpoint on the 2023 Rate Outlook: Will shippers catch a break? Global Labor Rates: China is no longer a low-cost country View More From this Issue
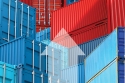